Кейс: искусственный интеллект для завода по производству деталей механообработки
На современных машиностроительных предприятиях даже незначительные отклонения в размерах деталей ведут к дорогостоящему браку, простоям и потере репутации.
Традиционные методы контроля (ручные замеры, выборочный ОТК) не успевают за скоростью станков с ЧПУ и часто пропускают дефекты. Как обеспечить 100% контроль качества без замедления производства?
Еще вчера ответ на этот вопрос был “никак”. Но сегодня с задачей успешно справляются системы на основе ИИ. В этом кейсе расскажем о разработке такой системы для нашего клиента.
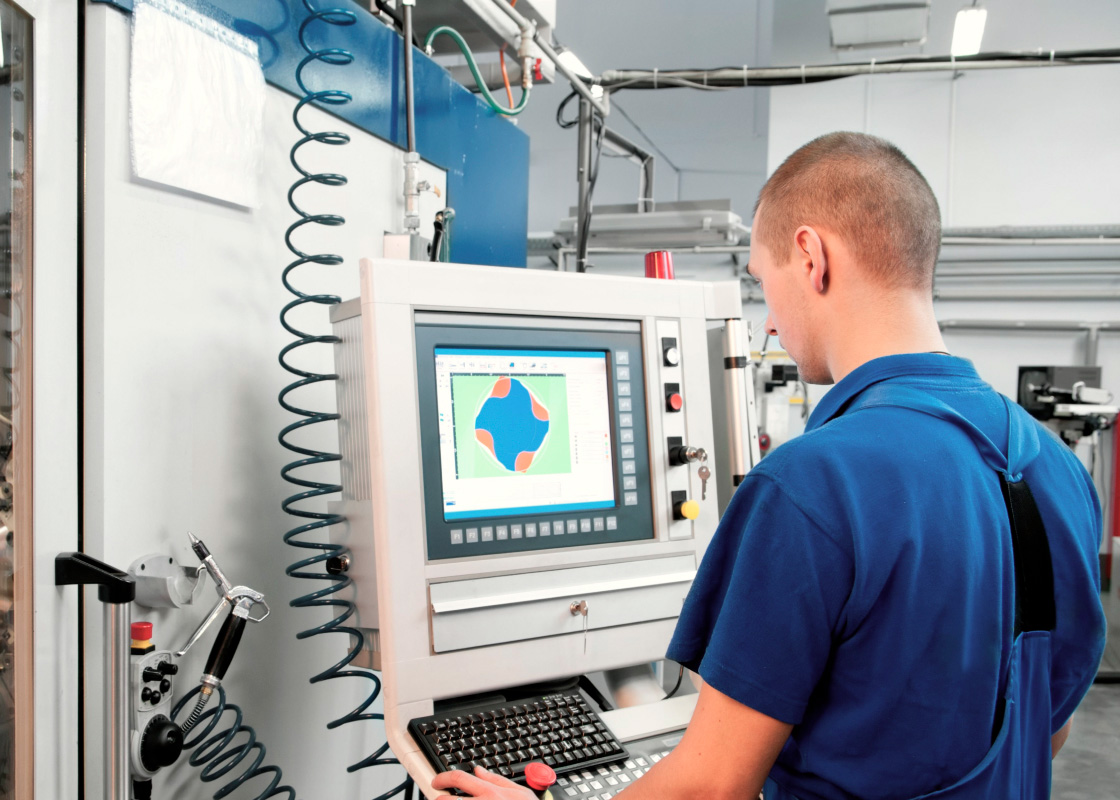
Клиент
Наш клиент в этом кейсе — крупный завод по производству деталей конвейерного оборудования.
Задачи
Необходимо было разработать ИИ-систему для контроля качества обработки деталей на станках с ЧПУ для автоматической отбраковки бракованных деталей и обеспечения соответствия продукции стандартам качества.
Зачем нужно использование искусственного интеллекта на заводе?
Искусственный интеллект трансформирует процесс проектирования, предлагая революционные возможности там, где традиционные методы уже не справляются.
1. Ликвидация «человеческого фактора»
Проблема: Даже опытные операторы ОТК устают и пропускают до 15-20% дефектов.
Решение: ИИ-визор (например, на базе CNN) анализирует 100% продукции без ошибок усталости.
2. Скорость контроля = скорость производства
Проблема: Ручные замеры тормозят линию — детали проверяются лишь выборочно.
Решение: ИИ-система обрабатывает больше изображений деталей без остановки конвейера.
Проектирование системы искусственного интеллекта для завода по производству деталей
Система, разработанная для нашего клиента, использует методы компьютерного зрения для измерения геометрических параметров деталей и определения дефектов.
После анализа производственных процессов и выявления ключевых точек, где возможны ошибки и дефекты, мы предложили клиенту комплексное решение, охватывающее четыре этапа контроля.
1. Входной контроль сырья
- 3D-сканирование заготовок для выявления отклонений перед обработкой.
- Автоматическая корректировка программы ЧПУ под параметры конкретной детали.
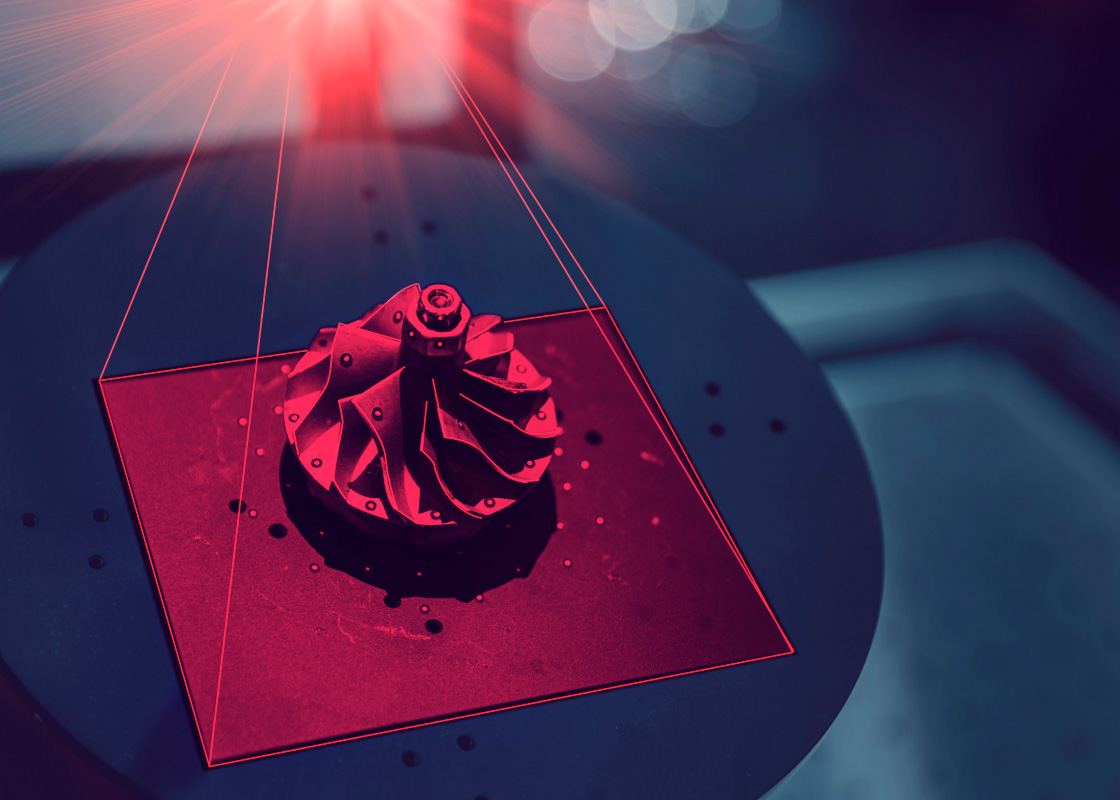
2. Контроль на уровне станка
На первом этапе мы установили систему в зоне ЧПУ-станков — непосредственно в месте изготовления деталей. Внутри рабочей зоны был установлен комплекс из камер и датчиков, обеспечивающий следующие функции:
- Анализ действий оператора: наличие защитного снаряжения (очки, перчатки), правильность выполнения технологической операции.
- Слежение за дисплеем станка: фиксация параметров, выставленных оператором, и их соответствие нормативам.
- Дистанционное измерение геометрических характеристик детали сразу после обработки (линейные, объемные размеры).
- Фиксация времени обработки и отслеживание соответствия технологии.
- Этот уровень контроля позволил выявлять ошибки ещё до того, как деталь покинула станок, что значительно снизило объём брака.
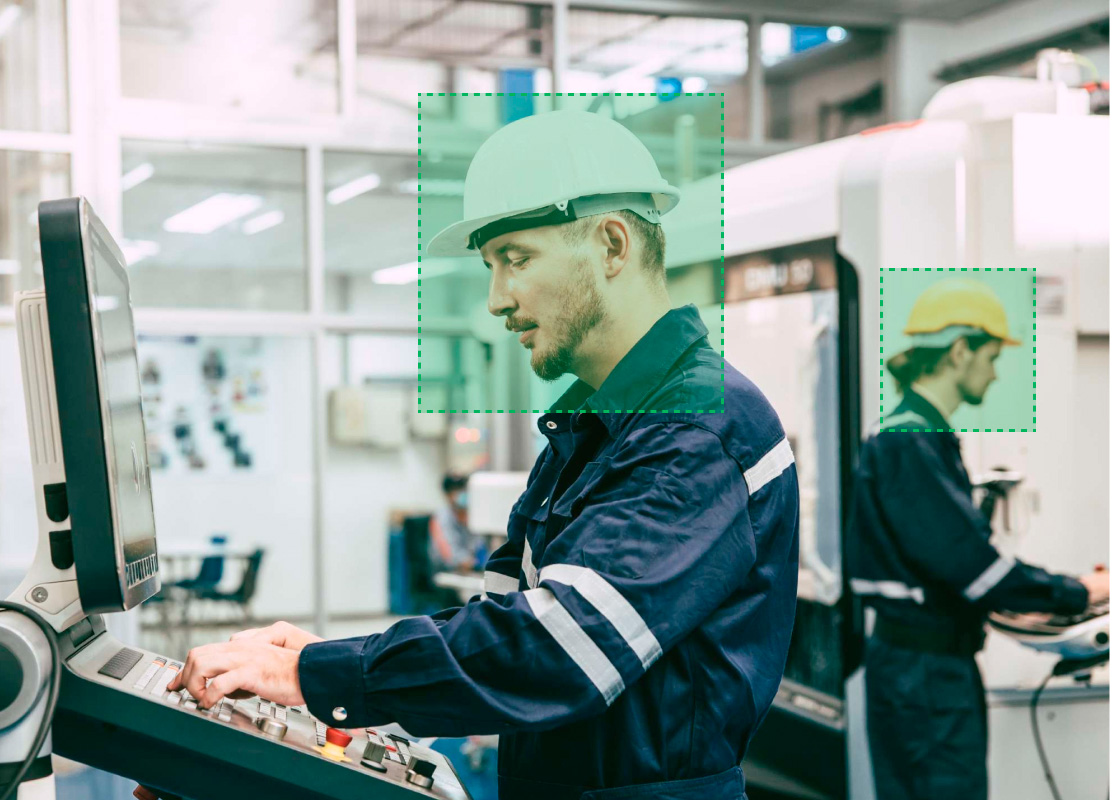
3. Контроль на транспортерной ленте
После выхода готовой детали из станка она перемещается на транспортерную ленту. Здесь была установлена камера высокого разрешения, которая:
- Отслеживает движение деталей на конвейере.
- Учитывает скорость ленты, чтобы не пропустить ни одну единицу продукции.
- Проверяет наличие внешних дефектов (царапины, сколы, трещины) и соответствие формы.
- Для обеспечения максимальной точности в этой зоне было организовано специальное освещение, исключающее тени и создающее "бестеневую зону". Это повысило качество обнаружения дефектов.
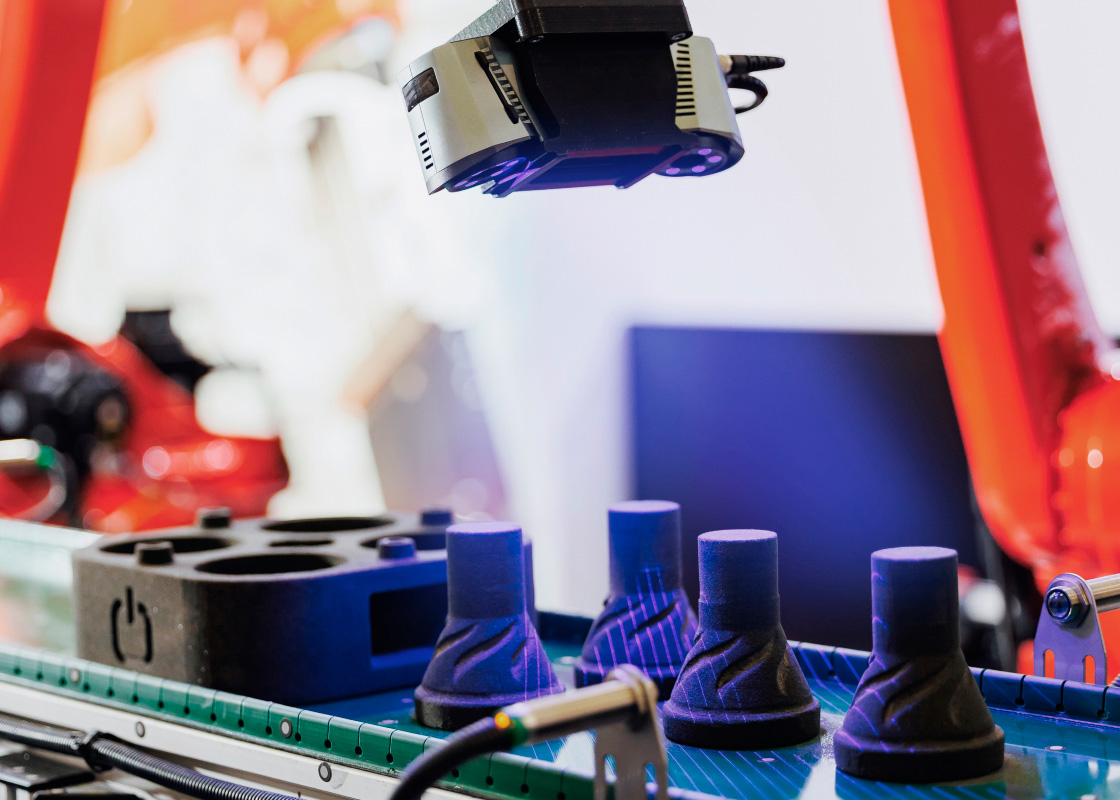
4. Выходной контроль и упаковка
Финальный этап контроля происходил в зоне упаковки. Здесь система выполняла полный анализ каждой детали по заранее заданным критериям:
- Проверка всех типов дефектов, перечисленных в техническом задании.
- Формирование отчета по каждой партии изделий.
- Интеграция с ERP-системой предприятия для автоматического учета результатов контроля.
Аппаратно-программная архитектура
1. Сенсорные системы
- Видеокамеры высокого разрешения для 3D-сканирования деталей и контроля их положения.
- Датчики вибрации, температуры и давления на станках для мониторинга состояния оборудования.
- Превентивное обслуживание: нейросети прогнозируют износ инструмента, сокращая простои на 30%.
2. Программная часть
- Нейросетевые алгоритмы для:
- Распознавания дефектов в реальном времени с точностью до 95%.
- Многоспектрального анализа (обнаружение микротрещин до 0,01 мм).
- Оптимизации траекторий инструмента (G-код) и параметров обработки.
- Экспертная система для диагностики оборудования и прогнозирования ТО.
- Модули компьютерного зрения с функциями:
- Сегментации изображений для выделения контуров деталей.
- Обнаружения стрингига и других дефектов в аддитивном производстве.
Методы контроля качества
1. Сравнение с эталонными моделями
- 3D-сканеры создают цифровую модель детали, которую нейросети сравнивают с CAD-шаблоном.
- Отклонения вычисляются по трём осям с точностью 0,01 мм.
2. Анализ геометрических параметров
- Видеокамеры фиксируют:
- Радиусы скруглений
- Углы фасок
- Соосность отверстий
- Алгоритмы на основе преобразования Хафа вычисляют параметры.
3. Контроль формы поверхностей
- Интерферометры выявляют волнистость и микронеровности.
- Тактильные щупы измеряют шероховатость (Ra/Rz).
- Для цилиндрических деталей применяются ротационные анализаторы биения.
4. Автоматическая классификация дефектов
- Свёрточные нейросети распознают 40+ типов дефектов (трещины, коробление, непровары).
- Используются предобученные модели с точностью 92–95%.
Техническая реализация
- Измерительные стенды с пневмозажимами и поворотными столами.
- Многоосевые манипуляторы для позиционирования датчиков.
- PLC-контроллеры, обрабатывающие сигналы с 100+ измерительных каналов.
- Протоколирование отклонений с цветовой маркировкой (зелёный/жёлтый/красный).
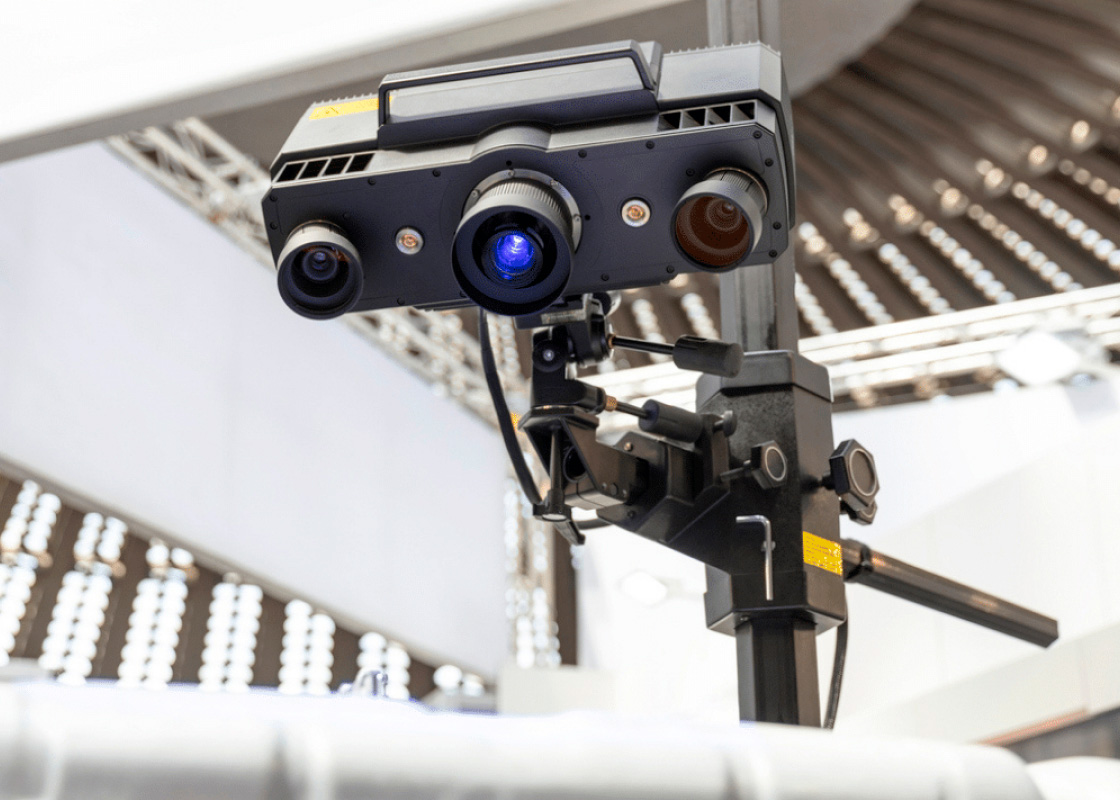
Этапы внедрения системы
Работа над проектом прошла несколько последовательных этапов:
1. Брифинг и диагностика.
- Мы провели встречу с представителями предприятия, изучили текущие проблемы и цели.
- Посетили производственные цеха, наблюдали за технологическими процессами, записывали всё на видео для последующего анализа.
2. Анализ условий.
- Оценили освещённость, задымлённость, наличие мешающих факторов в рабочих зонах.
- Зафиксировали процессы, которые могли быть автоматизированы (например, ручная передача данных).
3. Подготовка технического предложения.
- В течение 3–5 дней мы подготовили план реализации, подобрали необходимое оборудование и программное обеспечение.
- Обсудили с заказчиком все аспекты будущей системы, внесли корректировки.
4. Согласование и контрактование.
- Презентовали клиенту нашу концепцию, получили обратную связь.
- Уточнили требования, определили объём работ и подписали договор.
5. Проектирование и закупка оборудования.
- Подготовили подробное ТЗ для разработки программной части.
- Составили список оборудования, которое клиент мог закупить самостоятельно, чтобы сохранить гарантию.
6. Монтаж и интеграция.
- Помогли с установкой камер, датчиков и серверного оборудования.
- Интегрировали систему в существующую IT-инфраструктуру предприятия.
7. Тестирование и запуск.
- Провели тестовый запуск системы.
- Обучили сотрудников работе с новым интерфейсом.
- Перешли к полноценному режиму эксплуатации.
Как работает система? Примеры
Отбраковка деталей производится по ряду параметров:
1. Дефекты поверхности:
- Шероховатость: Неравномерность поверхности детали, вызванная следами режущего инструмента.
- Царапины: Глубокие, узкие борозды на поверхности детали, вызванные механическим воздействием.
- Задиры: Вырывы металла на поверхности детали, вызванные скольжением режущего инструмента.
- Заусенцы: Острые кромки металла, выступающие за пределы основной поверхности детали.
- Раковины: Углубления на поверхности детали, вызванные вырывами металла.
- Трещины: Разрывы в металле детали, вызванные внутренними напряжениями или механическим воздействием.
- Пятна: Потемнения или обесцвечивания на поверхности детали, вызванные коррозией или другими химическими процессами.
- Вмятины: Деформации поверхности детали, вызванные ударами или давлением.
2. Дефекты формы и размеров:
- Неправильные геометрические формы: Отклонения от заданных размеров и форм детали.
- Несоответствие размеров: Несоответствие размеров детали заданным значениям.
- Овальность: Несоответствие диаметра детали в разных сечениях.
- Конусность: Несоответствие диаметра детали по длине.
- Несоосность: Несовпадение осей отверстий или других элементов детали.
- Неперпендикулярность: Несоответствие углов между плоскостями или элементами детали.
- Биение: Качательные движения детали при вращении.
3. Дефекты обработки:
- Неправильные геометрические формы: Отклонения от заданных размеров и форм детали.
- Несоответствие размеров: Несоответствие размеров детали заданным значениям.
- Овальность: Несоответствие диаметра детали в разных сечениях.
- Конусность: Несоответствие диаметра детали по длине.
- Несоосность: Несовпадение осей отверстий или других элементов детали.
4. Дефекты материала:
- Посторонние включения: Неметаллические включения в металле, например, шлаки, оксиды, газы.
- Раковины: Углубления в металле, вызванные вырывами металла.
- Трещины: Разрывы в металле детали, вызванные внутренними напряжениями или механическим воздействием.
- Пористость: Пустоты в металле, вызванные газовыми пузырями или другими дефектами.
- Сегрегация: Неравномерное распределение элементов в сплаве.
5. Дефекты сборки:
- Неправильная сборка: Несоответствие деталей сборочному чертежу.
- Неправильная регулировка: Неправильное положение или зазоры между деталями.
- Нетермичность: Неспособность соединения выдерживать давление.
- Коррозия: Разрушение металла под действием окружающей среды.
- Износ: Постепенное разрушение поверхности деталей при трении.
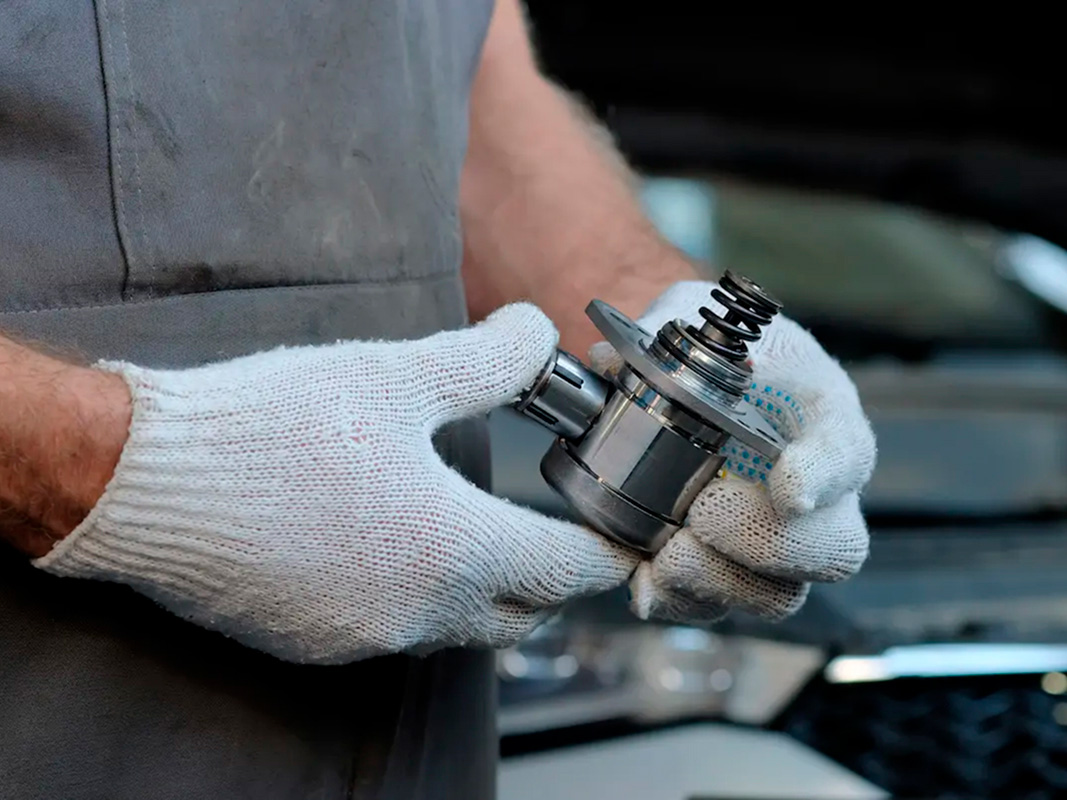
Результат внедрения системы искусственного интеллекта на заводе нашего клиента
Внедрение ИИ-системы позволило автоматизировать контроль качества, минимизировать человеческий фактор и перейти к безлюдным производственным циклам для серийных деталей. Технология демонстрирует высокую эффективность и масштабируемость для предприятий механообработки.
Результаты внедрения
- Сокращение времени перенастройки оборудования на 40% за счёт гибкой архитектуры.
- Уменьшение брака на 25–30% благодаря предиктивной аналитике и компьютерному зрению.
- Повышение точности обработки до IT7-IT8 за счёт динамической коррекции G-кода.
- Стабильная работа в сложных условиях (запылённость, перепады температур) с доступностью 95%.
- Снижение процента брака на 5–7% ежеквартально за счёт самообучения системы.
Кому будет полезно
Этот кейс будет критически важен производителям точных деталей, где брак приводит к огромным убыткам. ИИ-контроль на ЧПУ снижает дефекты, ускоряет проверку и обеспечивает соответствие строгим стандартам.
Нужна разработка системы с искусственным интеллектом?
Пишите, за 10 минут разберем задачи и рассчитаем примерную стоимость проекта.
Или звоните +7 (812) 925-77-70
Звоните, за 10 минут уточним задачи и рассчитаем примерную стоимость проекта.
тел.: +7 (812) 925-77-70